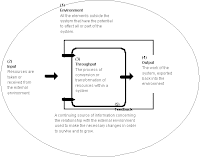
where Uin is the average internal energy entering the system and Uout is the average internal energy leaving the system
The region of space enclosed by open system boundaries is usually called a control volume, and it may or may not correspond to physical walls. If we choose the shape of the control volume such that all flow in or out occurs perpendicular to its surface, then the flow of matter into the system performs work as if it were a piston of fluid pushing mass into the system, and the system performs work on the flow of matter out as if it were driving a piston of fluid. There are then two types of work performed: flow workdescribed above which is performed on the fluid (this is also often called PV work) and shaft work which may be performed on some mechanical device. These two types of work are expressed in the equation:
Substitution into the equation above for the control volume cv yields:
The definition of enthalpy, H, permits us to use this thermodynamic potential to account for both internal energy and PV work in fluids for open systems:
During steady-state operation of a device (see turbine, pump, and engine), any system property within the control volume is independent of time. Therefore, the internal energy of the system enclosed by the control volume remains constant, which implies that dUcv in the expression above may be set equal to zero. This yields a useful expression for the power generation or requirement for these devices in the absence of chemical reactions: